Stock – Create And Edit Assemblies
Purpose:
Use this option to design manufactured and/or packaged items and control the stocks required to produce these items.
An assembly has its own stock code and location and consists of up to 50 components. Components can be Products, Services or Assemblies that have previously been created as stock items.
For example, Ian Competent PLC manufactures shovels. The components of a shovel are 1 wooden handle, 1 metal blade and 3 rivets. Ian buys each item separately from suppliers and then rivets the blade to the handle in his garden shed.
In his system Handles, Blades and Rivets are separate products. Ian uses the system to create an assembly as a separate stock item called shovel. Shovel is made up of the following components, Handle (1), Blade (1), Rivets (3) and Assembly time (a Service; 1 hour). Ian can now manage the stocks of each of the components of the shovel to ensure that he has sufficient stock of each piece of the shovel to meet customer demand. He can also manage the stocks of each component separately.
A Product, Service or Assembly can be a component of as many assemblies as the user needs. As each assembly can have 50 components, each of which can be an assembly itself, users can create multi-level complex assemblies that ultimately contain more than 50 Components. Assemblies are built from the bottom upwards, and a component must exist before it is incorporated into an assembly.
For further advice on designing assemblies, please consult your local Prelude distributor.
Preparation:
Select a company – see Change Companies.
Obtain a recent print of the existing Products or Services – see List Stock File Records.
Obtain the proposed selling price and standard cost of the assembly and details of any preferred supplier (as required if the assembly is manufactured by a Third Party for instance).
Obtain details of user-defined stock categories to allow assemblies to be grouped together for reporting purposes if required.
Set Minimum & Reorder Levels and Reorder Quantities for each assembly as necessary.
Obtain details of special prices and/or quantity discounts agreed with customers for assemblies.
For first time use only: On the main menu click View > Parameters > Stock Control – see Stock Control Parameters – General Page. Set parameters as required.
Processing:
To create a new Assembly:
On the main menu click Stock > Maintenance > Assemblies
Type in a new Assembly Code, (use up to 16 Alphanumeric characters). If using Multi Location Stock, enter the location code (2 characters). Click OK to open form.
Select an existing product to copy if required.
Complete the form as for individual products- see Stock Control – Product Maintenance Form.
Complete the components page- see Assembly Maintenance – Components Page below.
Click OK to update records and close form.
To amend an existing Assembly:
On the main menu click Stock > Maintenance > Assemblies.
Amend fields as required.
Click OK to update records and close form.
Filing:
Any source documents retained to be cross–referenced to stock code and dated.
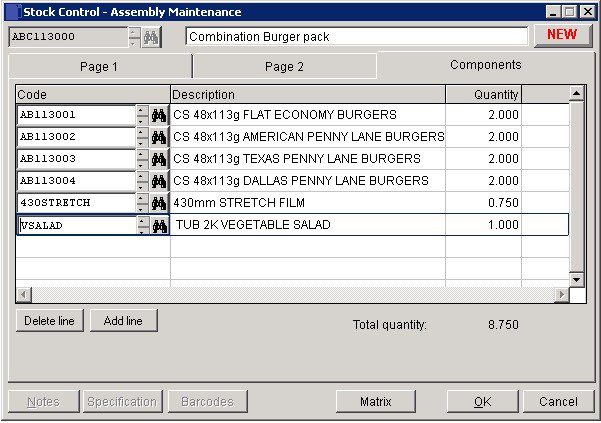
Refer to Product maintenance for details of pages 1 and 2.
Code: Select the components from the stock file – you can add labour and overhead costs into the stock file for selection.
OK to accept or Cancel to abandon.
0 Comments